

The Cherry E-Z Buck is a titanium/niobium rivet.Ĭherry rivets.- The generic Cherry rivet is a blind structural rivet with a locking collar for the stem installed as shown in figure 45. They generally do not need a coating for corrosion protection. Titanium/niobium rivets.- These titanium alloy rivets (per MIL-R-5674 and AMS4982) have a shear strength of 50 ksi but are still formable at room temperature. Monel is ductile enough to form a head without cracking but has higher strength ( F su = 49 ksi) and temperature capabilities than aluminum. Monel rivets.- Monel (67 percent nickel and 30 percent copper) rivets are used for joining stainless steels, titanium, and Inconel. The Cherry Buck rivet can be used to 600 ☏. This combination allows a shop head to be formed by bucking, but the overall shear strength of the rivet approaches 95 ksi. They can cause delamination of the hole surfaces, leading to material failure.Ĭherry Buck rivets.- The Cherry Buck rivet is a hybrid consisting of a factory head and shank of 95-ksi-shear-strength titanium, with a shop end shank of ductile titanium/niobium joined together by inertia welding (fig. Since solid rivets are expanded to an interference fit, they should not be used in composites or fiber materials. The 7050-T73 aluminum rivets are an alternative to "icebox" rivets. The "icebox" (DD) rivets can be used in higher-strength applications, but they must be kept around 0 ☏ until they are installed.
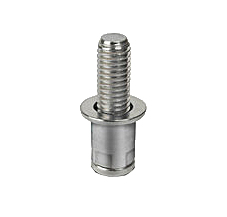
These are the preferred rivets for joining aluminums and combinations of aluminum and steel. A generic pull-mandrel rivet is shown in figure 36.ĪD & DD solid rivets.- The most common solid rivets are the AD and DD aluminum rivets, as listed in table IX. When the proper load is reached, the mandrel breaks at the notch. Pull-mandrel rivets: This rivet is installed with a tool that applies force to the rivet head while pulling a prenotched serrated mandrel through to expand the far side of the tubular rivet. Specific types (brands) of blind rivets are covered in subsequent sections of this manual.

Rivet bolt install#
Less training is required for the operator.īlind rivets are classified according to the methods used to install them: Installation time is faster than with solid rivets.Ĭlamping force is more uniform than with solid rivets. They can be used where only one side of the workpiece is accessible.Ī given-length rivet can be used for a range of material thicknesses.
Rivet bolt portable#
The installation tool is portable (comparable to an electric drill in size). Only one operator is required for installation. They have the following significant advantages over solid rivets: Note also that the countersunk head angle can vary from 60° to 120° although 82° and 100° are the common angles.īlind rivets.- Blind rivets get their name from the fact that they can be completely installed from one side. However, because the "experts" do not necessarily agree on the names, other names have been added to the figure. Although most of the solid rivets listed in table IX have universal heads, there are other common head types, as shown in figure 34. Note that the rivets in table IX are covered by military standard specifications, which are readily available. Table IX - Aluminum and Other Rivet Materials Some other solid rivet materials are brass, SAE 1006 to SAE 1035, 11 steels, A286 stainless steel, and titanium.
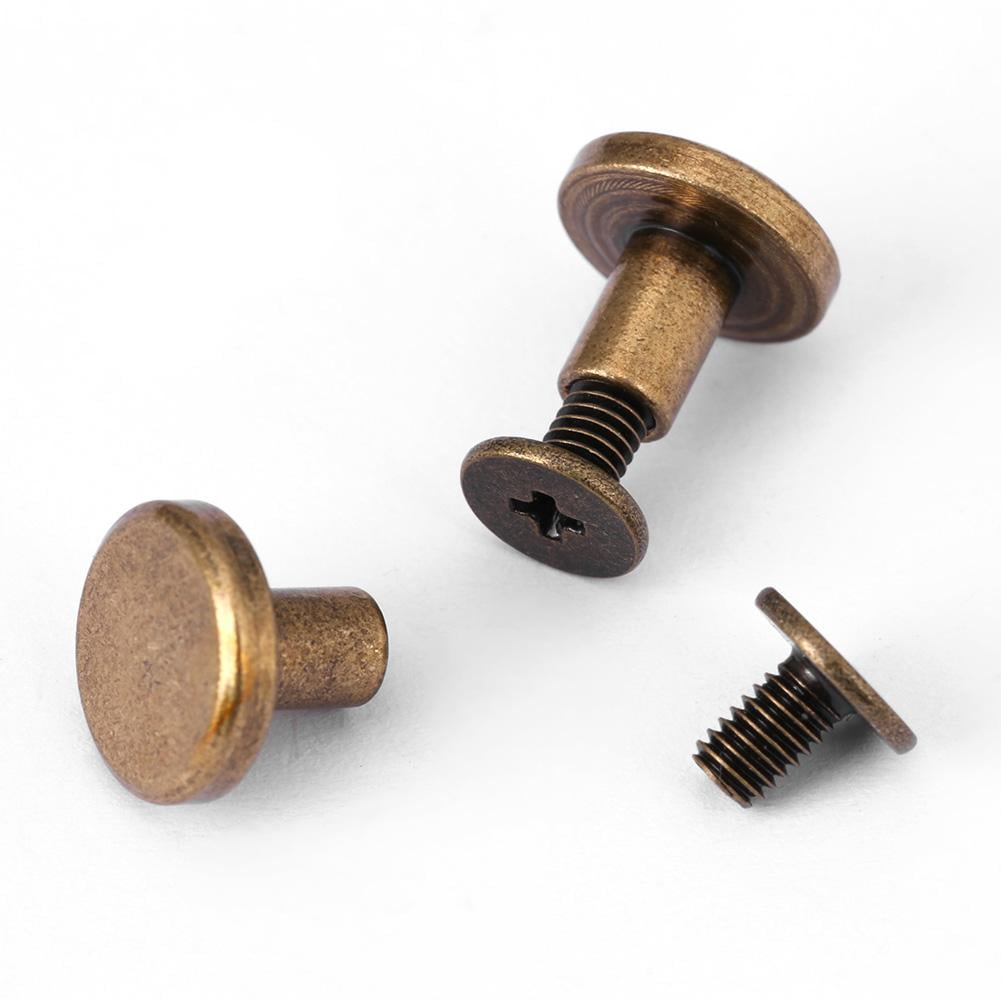
A representative listing of solid rivets is given in table IX (ref. Thus, solid rivets must have cold-forming capability without cracking. Solid rivets.- Most solid rivets are made of aluminum so that the shop head can be cold formed by bucking it with a pneumatic hammer. From a structural design aspect the most important rivets are the solid and blind rivets. The general types of rivets are solid, blind, tubular, and metal piercing (including split rivets). Since rivets are permanently installed, they have to be removed by drilling them out, a laborious task. Riveted joints are neither airtight nor watertight unless special seals or coatings are used. The longer the total grip length (the total thickness of sheets being joined), the more difficult it becomes to lock the rivet. However, rivets should not be used in thick materials or in tensile applications, as their tensile strengths are quite low relative to their shear strengths. They are faster to install than bolts and nuts, since they adapt well to automatic, high-speed installation tools. As a result, they are the most widely used fasteners in the aircraft manufacturing industry. Rivets are relatively low-cost, permanently installed fasteners that are lighter weight than bolts.
